Self-heating is one of the leading causes of fire and explosion in storing wood pellets. According to the 2021 Combustible Dust Incident Report, five fire and explosion events occurred in wood storage facilities in 2021, and most recently, in 2023, self-heating led to a fire in Japan’s Yonago biomass-fired power generation plant.
These types of incidents are believed to be initiated by temperature rise caused by moisture adsorption and condensation. The temperature increase is then accelerated when an oxidizable material, such as woody biomass, reacts to produce heat, which accumulates to a temperature of ignition and combustion. Self-heating is dangerous because when it is not controlled, fire and explosion can occur in biomass storage facilities and cause damage to health and property.
Over the past 20 years, researchers at the Biomass & Bioenergy Research Group (BBRG) at the University of British Columbia have carried out self-heating research, in parallel with off-gassing research. The research was funded by the Natural Sciences and Engineering Research Council of Canada (NSERC) and the members of the Wood Pellet Association of Canada (WPAC). Based on our research, we have developed six key steps pellet producers can take to prevent self-heating events:
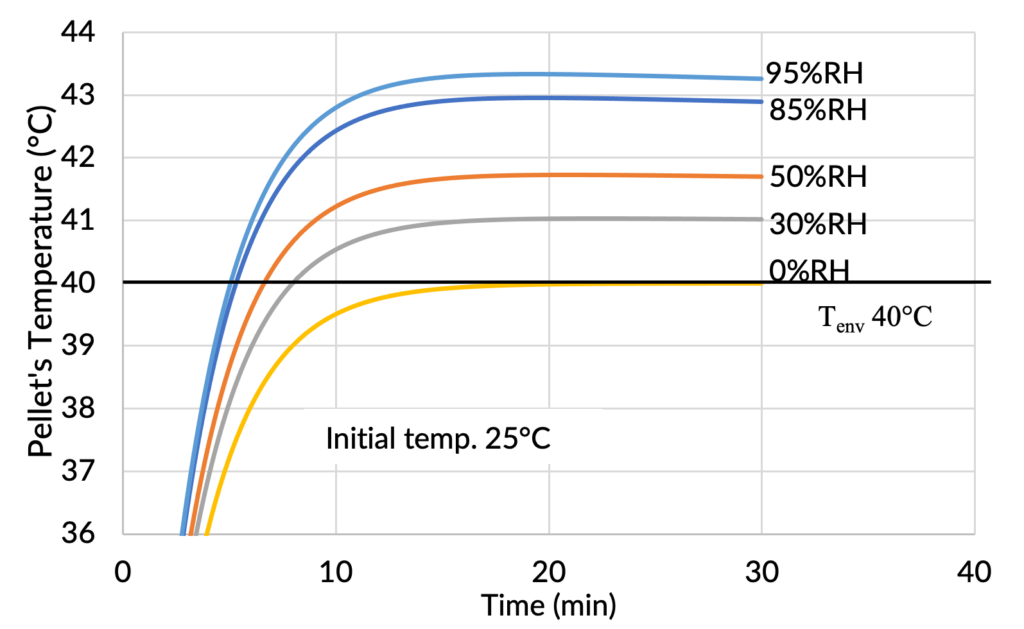
- Keep the pellets dry – but not too dry. Dry pellets adsorb more moisture than moist pellets. We recommend a moisture content of 7-8%.
- Do not store warm pellets in temperatures hotter than 35°C. Warm pellets reach self-heating conditions substantially faster than cooler pellets.
- Keep the pellets cool using ventilation but limit humid air as it can carry additional moisture into the silo. A higher air flow rate for a short time is preferred. However, if self-heating is already present, the introduction of air to the silo must be ceased immediately.
- Minimize loading broken and dust into the silo. Field experiences have shown that filing a silo at stages may create dense layers along the column of pellets inside a tall silo.
- Silo size is important. Generally, more slender structures dissipate heat faster than wide storage structures. Concrete silos come in 5, 7, 9 m diameter. Steel grain bins can be up to 18 m. Recommended silo diameter is 10 m or less.
- Screen pellets for reactivity using an instrument such as a Thermal Activity Monitor (TAM) which is available in BBRG’s lab at UBC. The unique instrument is used to determine the reactivity of pellets and to screen pellets for off-gassing.
Self-heating is not limited to just the wood pellet sector. This research can also provide important information for other products such as coal and agricultural biomass like straw and grass.
To find out more about our work, contact Shahab Sokhansanj via email at Shahab.Sokhansanj@ubc.ca.